汽车车身四层板焊接应用分析及存在问题
- 2017-05-24 13:16:00
- sawchina 转贴
- 8723
在目前的汽车车身(主要是乘用汽车、小轿车)设计中,为了保证车身焊接质量,通常不允许出现四层板焊接。由于此限制,需要增加过渡搭接头,从而增加了车身重量,影响车的性能,减少了车身设计的自由度。为了有效地对车身进行减重,改善车的性能并提高设计的灵活性,我公司对四层板电阻点焊进行了尝试,使其在汽车焊接中得到应用。
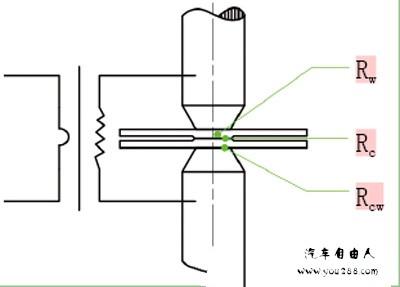
图1 电阻点焊中的电阻组成
电阻焊的原理
电阻焊是以电阻热为能源的一种焊接方法,焊接所需电阻热的产生遵守公式:Q=I2Rt,而电阻R由电极与工件的接触电阻Rcw、工件电阻Rw和工件与工件的接触电阻Rc组成:R=2Rcw+Rw+Rc,其中主要为电极与工件的接触电阻Rcw和工件与工件的接触电阻Rc,而这两部分主要取决于焊接压力。
四层板点焊试验
1.试验设计
根据电阻点焊焊接原理,将四层板点焊与两层板、三层板的焊接进行比较分析,其差别主要在于四层板的板间间隙难于控制,它的接触电阻相对不稳定,克服这些间隙需要较大的压力。板间的间隙和较大的压力的共同作用会使焊点的表面留下较深的压痕,甚至影响连接强度。 通过上述分析,我们进行试验,并进行比较,寻找合适的焊接参数和合理的检验判定标准。
(1)采用焊相同等效板厚的二层板的焊接参数范围焊接四层板,进行金相分析检查焊点的质量。在电阻点焊中通常以等效板厚作为参考来设定参数,这里以次厚板乘以0.8加上厚板乘以0.2作为等效板厚。
(2)逐步加大焊接压力,再用焊相同等效板厚的二层板的焊接参数(除压力)进行试焊,然后进行金相分析确定焊点的质量。
(3)加大压力,扩大焊接电流和时间范围,进行金相分析,寻找合理的参数范围。
2.试验结果
(1)采用焊相同等效板厚的二层板的焊接参数范围焊接四层板,经过金相分析发现在这种条件下的焊点质量极不稳定,不易形成稳定的熔核直径,且容易出现气孔缺陷。使用与焊相同等效板厚的二层板的焊接压力,其可用参数范围很窄,且不稳定。在逐步加大焊接压力,多次试验后,发现当电极压力是相同等效板厚的二层板焊接时的120%~130%时,可以在一定范围内得到稳定的熔核直径,获得较稳定的焊接质量,但其压痕较深,飞溅不易控制。
(2)当电极压力增加到相同等效板厚二层板的焊接压力的130%后,电流的调整范围不再明显扩大,电极压力的增大加大了电极损耗,造成了更大的焊点压痕。
选取的是0.8+1.2+1.4+0.8mm的板厚搭配,在焊接参数为 14CYC、3.7kN(相同等效板厚的二层板焊接压力通常取2.5~2.8kN)和电极端面直径5.5mm左右时,采用不同的焊接电流所得到焊接。
3.试验结果分析
在14CYC、3.7kN以及电极端面直径5.5mm条件下采用不同的焊接电流所得到焊接金相结果数值如表所示,从试验
(1)可以看出试验结果与理论分析是基本吻合,由于四层板配合的间隙难以控制,与相同等效板厚的两层板焊接相比,需要较大的焊接压力(比通常情况大20%~30%),才能得到稳定的焊接质量。
结合试验(2)、(3),可以得知四层板仍是可以焊接的,但分析表中的可用参数范围与相同等效板厚的两层板焊接的参数范围比较,四层板焊接的可用参数范围相对较小。以0.8+1.2+1.4+0.8mm的板厚搭配为例,可用电流范围为8.5~9.8kA,差值为1.3kA,与相同等效板厚的两层板焊接相比,可用电流范围略小(相同等效厚度的两层板焊接时的电流差值可达1.5kA)。
同时,从试验结果中可以看出,四层板焊接时,焊点的压痕较深,剩余板厚相对较小。
因为焊点压痕深度会影响到焊点的动态疲劳强度,因此在点焊焊点的检验标准中,通常会对焊点的压痕深度作出规定,较常见的规定为板厚的30%,但是由于是多层板,加上间隙的影响,使得与电极接触的各板的焊点压痕深度大于板厚的30%。如果将检查标准中对压痕深度的要求更改为对剩余板厚的要求,如规定为剩余板厚不小于总板厚的70%,则是具有可行性的。
但是由于外层板上的压痕较深会降低外侧板焊点的动态疲劳强度,因此,在产品车身设计阶段需要考虑此因素,如增加焊点数量、焊点周围加涂胶液等。通过产品的模拟分析并经过实际验证后,证实此方法是可以在后续的产品中应用的。在产品设计时充分考虑到焊点压痕深度对动态疲劳强度的影响,并改进相关评价标准的情况下,四层板焊接是可行的。
这为车身零件间搭接头的设计又提供了一种选择,增加了设计的灵活性,有利于减轻车身的重量。但需要注意以下几点:焊接压力比通常情况下大20%~30%;焊接的热量范围略小于通常情况;焊接的波动相对较大,需要特别注意;焊接飞溅相对较大。
相关文章
- [焊接百科] 大熔深GTAW焊 2015-11-17
- [焊接百科] 钨极惰性气体保护焊(GTAW)的改进形式 2015-11-17
发表评论
社区新帖
- GBT 19867.4-2008 激光焊接工艺规程.pdf 2019-12-25
- GBT 2652-2008 焊缝及熔敷金属拉伸试验方法.pdf 2019-12-25
- GBT 16672-1996 焊缝-工作位置-倾角和转角的定义.pdf 2019-12-25
- GBT 16745-1997 金属覆盖层产品钎焊性的标准试验方法.pdf 2019-12-25
- GBT 17853-1999 不锈钢药芯焊丝.pdf 2019-12-25
- GBT 15169-1994 钢熔化焊手焊工资格考核方法.pdf 2019-12-25
- GBT 15579.5-2005 弧焊设备安全要求 第5部分 送丝装置.pdf 2019-12-25
- GBT 15579.7-2005 弧焊设备安全要求第7部分:焊炬(枪).pdf 2019-12-23
联系我们
联系人: | 韩玉琦 |
---|---|
电话: | 0755-26013200/26013464 |
传真: | 0755-26013188 |
Email: | saw@sawchina.cn |
QQ: | 2280915288 |
微信: | 18682260315 |
旺旺: | szhbkj |
地址: | 东莞市凤岗镇东深路凤岗段206号天安深创谷W2栋诚信大厦21楼 |